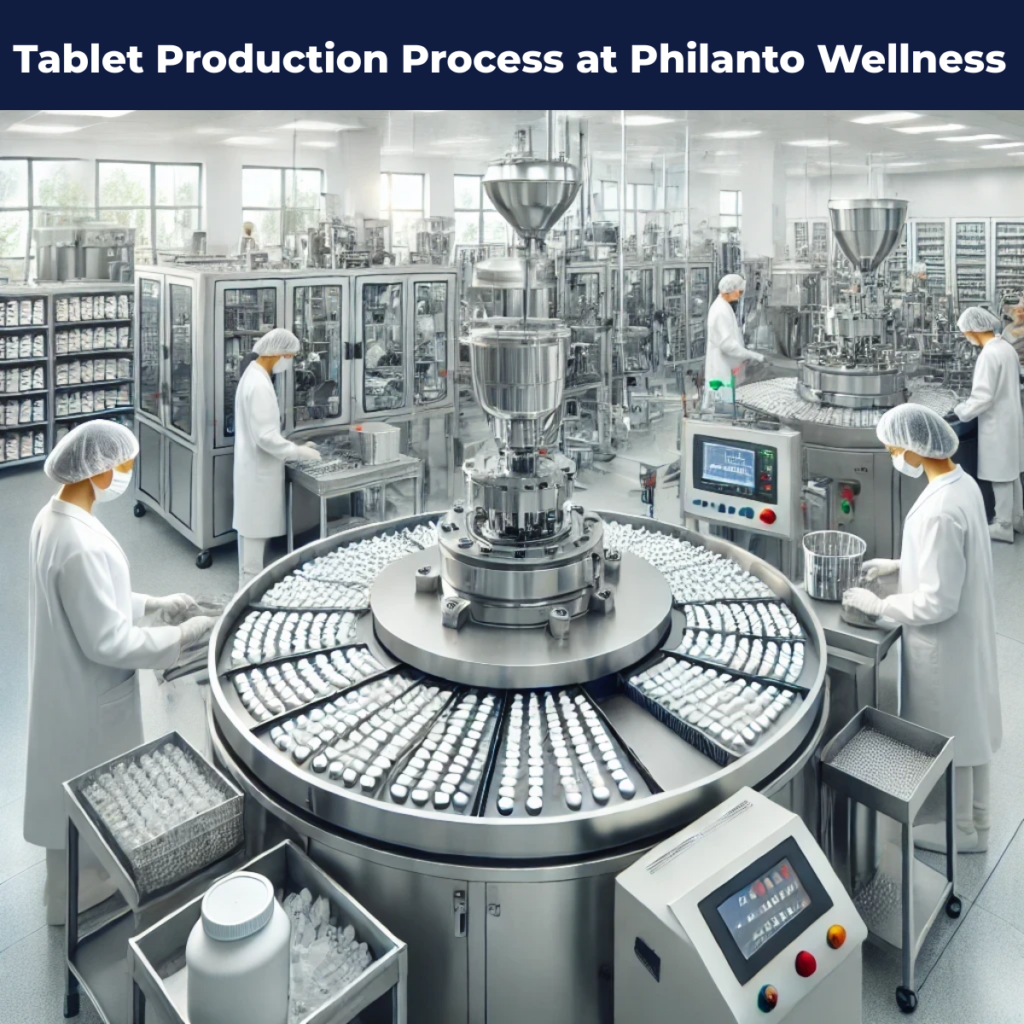
Philanto Wellness is a pharmaceutical company with WHO-GMP (World Health Organization Good Manufacturing Practices) certification that manufactures quality tablets. Production is done with strict adherence to international procedures in place to ensure that all the tablets that we manufacture are safe, and effective and undergo strict QC control. In this text, we describe the detailed Process of Tablet Manufacturing at Philanto Wellness while at the same time bringing to attention the essential points within the process that will guarantee the best quality possible in the industry.
1). Raw Material Procurement and Inspection
The first order of business in tablet formulation is the acquisition of raw materials of the highest quality possible. There are those known as Active Pharmaceutical Ingredients (APIs) and these are the chemical constituents that are active and thus bring about the therapeutic aspect then there are Excipient chemicals that are inactive and assist during tablet compression.
Some other methods of obtaining API resources from some manufacturers include: providing patients with the medicines and conducting their reports Pillar funds are spent on drug testing usually done in a limited capacity for the health and safety resources. In the case of Philanto Wellness, all the raw materials are acquired from approved and certified suppliers and then tested for several parameters in the quality control (QC) departments. These tests are meant to confirm that the materials conform to a particular standard in terms of purity, identity and potency. Only upon satisfactory completion of these tests can those raw materials be passed for employment in the process of production.
2). Weighing and Dispensing
Upon approval, the raw components are correctly dispensed and weighed out in the quantities specified in the formulation documents. This is essential because if the amount of the active ingredients, even in small quantities, varies from the set standard, it may adversely affect the potency of the tablet. At Philanto Wellness, they have mounting systems that are automated to guarantee correctness and avoid rounding at this stage.
3). Granulation Process
Granulation is the ability of powder to be pressed or made into granules which are more convenient to handle as well as compress into tablets. There are two categories of the granulation process:
- Wet Granulation: Wet granulation is the method that starts with adding a granulating liquid to the ingredients to develop a wet mass. After this, a drying step is applied followed by a sieving step to yield granules of equal sizes. Most of the tablets are manufactured through the wet granulation method to enhance compressibility.
- Dry Granulation: For moisture-sensitive materials, dry granulation is employed. In this technique, the bulk density of the powdered ingredients is increased by pressing them into larger bits that then get pulverized into granules.
4). Blending
Upon completion of granulation, the granules are produced into granules, which is important in achieving uniformity in the active ingredient distribution as well as excipients. This is a very important step since if there is too much cement mixture in some tablets and less in some it may affect the result of the product.
At the facility, the latest technology of blending has been incorporated which ensures that the end product received is not less than what is expected.
5). Tablet Compression
The granules that have been subjected to blending are charged in the tablet presses to form the tablets of the required shape. In this stage, the tablet size, shape and hardness as well as the thickness of the tablet are explained all in totality, in a bid to attain uniformity.
This process is carried out with great attention to make sure that every single tablet amounts to the required dose and fits into the acceptable weight, shape and hardness. Our state-of-the-art tablet press machines allow the production of tablets in whatever shape and size that the client specifies.
6). Coating Process (Optional)
The tablets that are meant for oral intake can be coated for other reasons and some are given coating because of these and those.
- A coating masks the taste of undesirable active material.
- A tablet coating is necessary to protect the active pharmaceutical ingredient from adverse environments such as humidity and light.
7). Quality Control Testing
Every batch of tablets produced passes through distinct stages of production quality control to assure compliance with international standards, including the following:
This includes specific tests for every batch of tablets weighing uniformity, tablet hardness, disintegration time, dissolution rate concerning time taken for a tablet to dissolve and release the required active ingredient in the body internally etc., and the colour’s uniformity.
There is an internal quality control (QC) at Philanto Wellness to meet these requirements with optimal control. The tablets are approved for packing after full clearance of all the QC tests.
8). Packaging
After they have been subjected to all the quality control tests recommended, the tablets undergo packing in areas where there is no possibility of contamination. We can carry out packaging using blister packs, bottles, epoxy resin, and strip packs to cover the gaps in different markets.
The packaging processes and techniques at Philanto Wellness are meant to ensure that the tablets are free from adverse conditions such as moisture and air which would have otherwise reduced their shelf life and effectiveness.
9). Storage and Distribution
Storage and Distribution Considerations After sterilization, the tablets are stored in the warehouses under regulated temperature and humidity conditions. This helps in maintaining the tablets’ stability in their active state through the expected life span. Our logistics ensure that from there, the tablets are distributed to primary health care, chemists, etc. safely.
Why WHO-GMP Certification Matters
Philanto Wellness’s WHO-GMP certification permits only the best suitable drugs for marketing due to strict manufacturing regulations. With regards to our focus on quality, this certification is the evidence of our statement. By following these parameters, we make sure that there are no unwanted particles included in our tablets, the tablets meet the designed specifications and the tablets can be traced back in the supply chain. Certification reflects our philosophy of improvement and modernization in the manufacturing of drugs.
Conclusion
we are proud of the complete tablet manufacturing process which is WHO-GMP compliant at Philanto Wellness. Committed at every stage of the process, in the selection of reasonable raw materials as well as granulation, blending, compression, and package technologies to worldwide standards of safety and efficiency.
[…] Also Read : Tablet Manufacturing Process […]