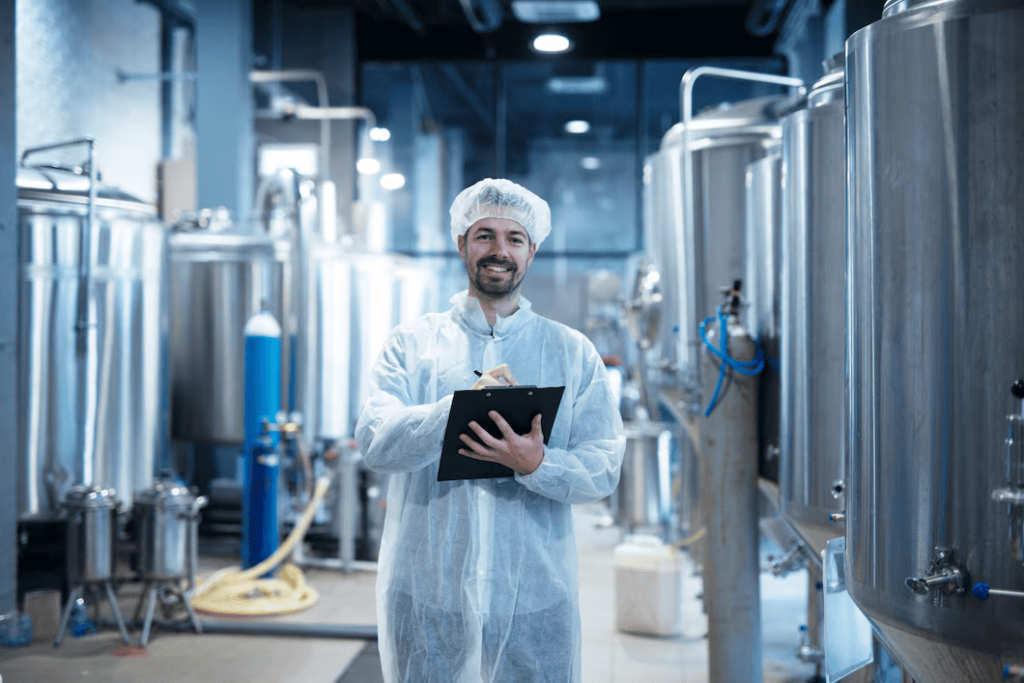
The pharmaceutical welfare industry is connected with public health as it manufactures medicines for disease treatment, symptom alleviation and enhancing the quality of life. The usefulness and safety of these medicines are highly accurate depending on the well-instituted quality control (QC) processes. Quality control in pharmaceutical manufacturing refers to the measurement of each component against precise approval criteria and controlling standards that ensure, in this case, the safety of patients and the quality of public trust.
Those issues will be discussed in this article, focusing on the importance, steps, and challenges of quality control in pharmaceutical manufacturing, analytical methods, and Good Manufacturing Practices (GMP) compliance.
The Importance of Quality Control in Pharmaceutical Manufacturing
As discussed above, there are several vital reasons why checkpoints are very crucial in pharmaceutical quality control practices;
- Patient’s Health Security: The most important essence of QC is providing peace of mind that any medicine is safe for use. Safe use can easily be questioned if there are loophole discrepancies in the level of deviation59.
- Legal Compliance: A legal entity such as a pharmaceutical company must follow rules designed by governing figures like the FDA, EMA and ICH. Not following this can open a door for product returns, court costs, and bringing detriment to the image of a firm29.
- Sample Standardization: QC ensures that every batch of a drug is consistent in strength, purity, and efficacy, providing reliable therapeutic outcomes
- Public Trust: High-quality products build consumer confidence and enhance the reputation of pharmaceutical companies
Important Parts of Quality Control in the Pharmaceutical Industry
To maximize efficiency, quality control in pharmaceutical manufacturing employs a step-by-step strategy to guarantee that every product meets quality standards throughout the entire production process:
- Testing of Raw Materials: The quality control process starts by identifying materials to ensure that they are uncontaminated and comprise them. Low-quality materials might lead to low-quality end products.
- Testing during Production: In the course of the production, parts of the product that have already been produced are made to confirm they comply with quality definitions. Doing this prevents the production of products that deviate from the set standards.
- Final Examination of Product: All sold products are tested extensively and thoroughly to check whether safety, effectiveness, and quality measures are looked after. Products that are proven to be acceptable throughout these tests should not be kept in storage.
- Analysis of Stability: In various environmental conditions, certain products are stored for a particular timeframe to observe the changes and assess the suitability of the determined shelf life and storage suggestions.
- Accountability and Record Keeping: Report transparency and conformability to regulations are ensured by requesting and logging all procedures, examinations, and results.
Issues Encountered in Pharmaceutical Quality Control
The importance of implementing Quality Control in the Pharma Manufacturing of pharmaceuticals is not easy due to the following challenges:
- Changing Regulations: Some information updates from regulators continuously change with time and industries, and this makes it hard for companies to operate on an inflexible basis.9
- Difficult Supply Chains: It may be difficult to assure that the quality of the raw materials obtained from several suppliers is satisfactory.9
- Costly: The new technologies for QC integration and consultant services, in addition to meeting the standards of GMP, may cost a lot.9
- Mistakes: Even after strict supervision and extensive training, people make mistakes in testing and documentation, which puts the quality of the product at risk.
Final Thoughts
The Manufacturing of pharmaceutical products would be impossible without their analysis and control in quality measures, which guarantees that products are available to patients ready to be used safely and effectively as well as administered precisely. Following GMP rules and developing strict QC control systems allows pharmaceutical companies to operate within the rules made, safeguard the health of patients, and maintain the faith of the public. In the forecast, new technologies or permanent improvements in quality control will be needed for meeting the industry expectations and solving the issues at hand.