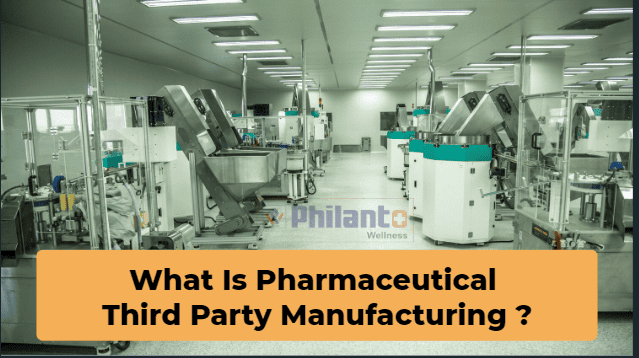
Pharmaceutical third party manufacturing, also known as contract manufacturing, is a service provision in the pharmaceutical industry where a firm hires a separate manufacturing company to produce its pharmaceutical products. This external company is responsible for the actual formulation and production of the drugs, following the hiring firm’s specifications, quality standards, and ensuring compliance with relevant regulatory requirements.
Here’s how third party pharmaceutical manufacturing typically works:
- Product Ordering: The client company, which has the formula and rights to a pharmaceutical product, approaches the third party manufacturer with an order to produce a specified quantity of the product.
- Quotation and Agreement: The third-party manufacturer provides a quotation detailing the costs involved. Upon agreement, both parties finalize a contract outlining the terms of the manufacturing arrangement, including timelines, quality standards, and cost.
- Supply of Raw Materials: Depending on the agreement, the client may supply the raw materials and active pharmaceutical ingredients (APIs), or the manufacturer may procure them on behalf of the client.
- Production: The third-party manufacturer produces the drug products in their facility, adhering to the legal and quality requirements, such as Good Manufacturing Practices (GMP).
- Quality Assurance and Control: Throughout production, quality assurance processes are in place to ensure that the product meets defined standards. This step includes testing batches, validating processes, and ensuring product stability.
- Packaging and Labeling: Once the product passes all quality tests, it is packaged and labelled as per the client’s specifications or regulatory requirements.
- Delivery: The final pharmaceutical products are delivered to the client or, as per some agreements, directly to the distributors or retailers.
Pharma third party manufacturing enables companies that do not have their manufacturing facilities, or that might want to outsource production due to cost considerations, capacity issues, or logistical reasons, to bring their products to the market. It is a cost-effective approach that allows pharmaceutical firms to focus on their core activities like drug development, marketing, and sales, while the complexities of production are handled by external specialists.