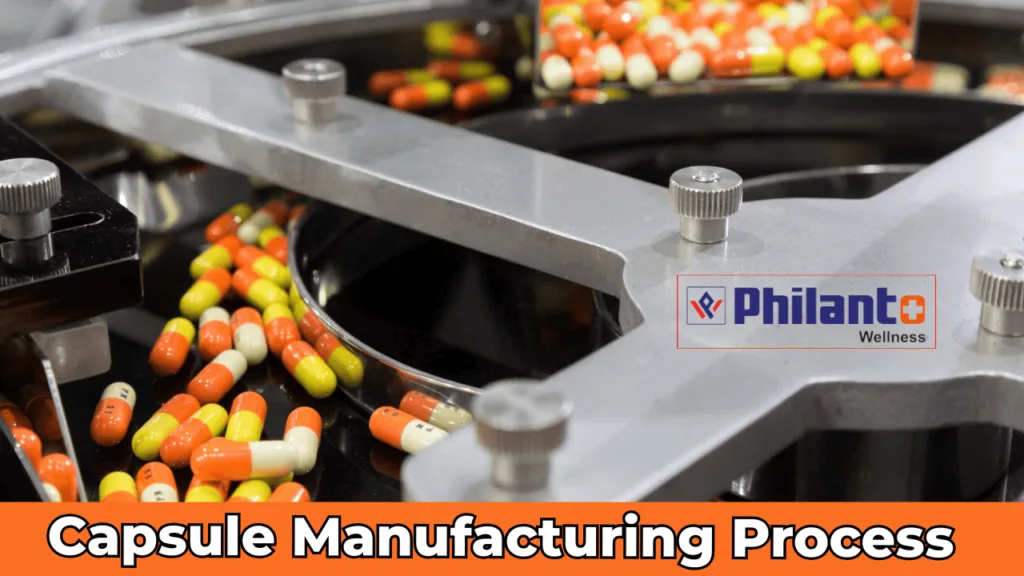
Capsules are one of the most common and efficient drug delivery forms in the pharmaceutical industry. At Philanto Wellness, a WHO-GMP-certified company, we specialize in manufacturing high-quality pharmaceutical capsules that meet international standards. This article provides an in-depth look at the capsule manufacturing process, from raw material selection to final packaging.
Step 1: Raw Material Selection
The first step in capsule manufacturing is selecting the appropriate raw materials, which primarily include active pharmaceutical ingredients (APIs) and excipients. APIs are the primary ingredients responsible for the therapeutic effect, while excipients help in processing the capsule and enhancing its stability, bioavailability, and appearance. Philanto Wellness ensures that all raw materials are of the highest quality, meeting both domestic and international regulatory standards.
Step 2: Mixing and Blending
Once the raw materials are procured, the next step concerns mixing and blending the API with excipients. The goal is to create a homogenous mixture to ensure that each capsule contains the correct dosage of active ingredients. Various methods, such as dry blending or wet granulation, may be used depending on the type of capsule being produced.
Philanto Wellness employs state-of-the-art machinery for accurate and uniform blending. Quality control checks are performed at this stage to ensure consistency and prevent dosage errors.
Step 3: Encapsulation
The encapsulation process involves filling the mixture into the capsule shells. Capsules are typically made from gelatin or a vegetarian substitute like hydroxypropyl methylcellulose (HPMC). There are two main types of capsules:
- Hard Gelatin Capsules: These consist of two halves, with the powdered or granular drug-filled inside.
- Soft Gelatin Capsules: These contain liquid or semi-solid drugs enclosed in a soft shell.
The capsule-filling machines at Philanto Wellness are fully automated, allowing for precise filling with minimal wastage. The process is tightly controlled to ensure that each capsule is uniform in weight and content.
Step 4: Capsule Sealing
In some cases, capsules need to be sealed to prevent tampering or leakage. While hard gelatin capsules typically don’t require sealing, soft gelatin capsules often undergo this step. Philanto Wellness employs advanced technology for hermetically sealing soft capsules to maintain their integrity throughout the product’s shelf life.
Step 5: Drying
After encapsulation, soft gelatin capsules are dried to remove any residual moisture that could affect their stability. Drying is a crucial step, as moisture can lead to spoilage or degradation of the active ingredients. Capsules are dried under controlled conditions, and moisture levels are continuously monitored to ensure optimal quality.
Step 6: Polishing and Sorting
Once the capsules are dried, they are polished to remove any excess powder or irregularities. This step enhances the appearance and ensures that the capsules are clean before packaging. Capsules are also sorted to remove any defective units, ensuring that only those meeting the highest quality standards proceed to the next phase.
Step 7: Quality Control and Testing
Quality control is an integral part of the capsule manufacturing process at Philanto Wellness. At multiple stages, capsules are tested for:
- Weight uniformity: Ensuring that each capsule contains the correct amount of medication.
- Disintegration and dissolution: Checking that the capsules release their contents as intended once ingested.
- Content uniformity: Verifying that the active ingredient is evenly distributed within the batch.
- Stability: Testing the capsules under various environmental conditions to ensure shelf life.
Our in-house laboratories are equipped with cutting-edge technology to perform these tests, ensuring that our capsules meet both regulatory and customer expectations.
Step 8: Packaging
The final step in the capsule manufacturing process is packaging. Depending on client requirements, capsules are packed into blister packs, bottles, or other containers. At Philanto Wellness, we use tamper-evident packaging to guarantee product safety and authenticity.
In addition to protecting the product from environmental factors such as light, moisture, and air, packaging also provides essential information, including dosage instructions and batch numbers for traceability.
Also Read : Tablet Manufacturing Process
Compliance with Regulations
As an organization that deals with drugs and medical devices, Philanto Wellness works according to stringent pharmaceutical regulations, e.g. WHO-GMP, which means that every single operation of the capsule production process meets universal requirements. Regardless of the product type, whether the raw materials or finished products, we always emphasize the provision of quality and safe pharmaceutical products to our clients.
Why Choose Philanto Wellness for Capsule Manufacturing?
In the pharmaceutical sector, capsule manufacturing services contain the renowned name Philanto Wellness. Located in Derabasi, Punjab with state-of-the-art facilities, and professional staff, we assure quality at every level in the processes. Our tailored services effectively meet diverse needs such as Third Party Manufacturing, and contract Manufacturing.
Conclusion
The manufacturing of capsules involves a number of processes and activities, which in turn require very careful monitoring controls and manipulations if the quality of the end products is to remain constant. Handling, production, and development of capsule forms is simplified in Philanto Wellness. Our potent technology, high-level quality control through multiple systems and strict adherence to regulations are the ingredients of trust that you should have in us regarding the manufacturing of capsules.